A key project in the 13th five-year plan of the Hubei power grid, the Xudong underground substation is central China’s first fully underground 220-kV substation and the closest substation to the Yangtze River. Located in the heart of the business and cultural district of Wuhan, amid a dense residential area, the station is being built underground to integrate better with the surrounding environment. The facility will create a beautiful park-like setting, coordinating with the ground green landscape. Its completion will meet the electricity demand of the ambient area.
The project is a pilot demonstration for Wuhan to build a first-class power grid and provide electricity for 200,000 residents in the northern urban area of Wuchang, improving power supply reliability and supporting city development. Powerchina Hubei Electric Engineering Co Ltd (HEEC) is delivering the project for China’s State Grid Corporation, who required that the substation be designed and built as a national leading and highly intelligent underground power supply complex. “This project represents the most advanced design of a 220-kV underground GIS substation of the State Grid Corporation,” said Wei Wang, deputy general manager, digital branch at HEEC.
Design, construction and maintenance challenges
Being built entirely underground in an urban area, the substation presented a compact footprint, compounded by a short construction schedule and multiple disciplines that required significant coordination. The site layout was extremely limited by the densely distributed buildings and surrounding landscape. Additionally, the substation adopted thousands of power, fibre optic and secondary control cables, making it challenging to arrange them all within the small space.
As the substation is located adjacent to the Yangtze River, the excavation depth and underground water pressure added to the design and construction difficulties, requiring rational, coordinated planning among all stakeholders and participants. “There were too many participants involved, which [made it] difficult to collaborate,” said Mr Wang.
To improve design quality, reduce rework on site, and meet the tight construction timeline, HEEC wanted to adopt 3D digital collaborative design for all disciplines and processes. The team planned on using the 3D design models to effectively guide construction and handing over digital deliverables to the State Grid Corporation for operations and maintenance. The team tried using traditional AutoCAD software during the initial design.
However, while AutoCAD helped resolve challenges in the early manual drawing stage, the software was unable to satisfy collaborative multidiscipline design and information exchange throughout the construction process. “It was a major challenge to consider the very tight construction period, as well as how to efficiently cooperate with all the participating units to complete the construction and management in a safe and high-quality manner, and to ensure that the substation is put into operation on time,” said Mr Wang.
In addition, HEEC wanted to improve efficiency and safety during operations and maintenance. The lack of a visual digital substation management platform prevented the owner and operators from accurately and proactively identifying and addressing equipment issues. HEEC realised that it needed an integrated technology solution to streamline design and construction workflows. The team sought to develop a digital twin that could be used for equipment monitoring and intelligent substation operation and management.
Leveraging Bentley’s integrated technology
After considering its options, HEEC selected Bentley’s ProjectWise as its collaborative design management platform. Combined with Bentley’s 3D BIM and reality modelling applications, HEEC customised the software to develop a full lifecycle underground substation design solution. Integrating aerial drones to capture the surrounding substation area, the team developed an accurate reality mesh, facilitating station site planning to accommodate the compact layout.
“Compared with the traditional 2D drawings, the reality model can intuitively reflect the topography, vegetation, rivers and lakes, roads, houses, and other information of the substation area,” said Mr Wang. Using Bentley’s open 3D modelling applications, HEEC performed coordinated design and collision detection to optimise substation building arrangement and layout of the equipment, cable and piping scheme. “The Bentley solution is the perfect idea to many problems encountered in the design of underground substations, such as space arrangement, equipment collisions and pipe access,” said Mr Wang.
Importing the design models into Synchro and LumenRT, HEEC performed construction simulation to help improve construction quality and efficiency, supporting construction management. On-site workers had access to the 3D models remotely via tablets and Bentley’s mobile applications, providing real-time insight into the design and construction process. The digitally integrated solution enabled precise calculation of bills of quantity and earthworks, as well as eliminated costly and time-consuming on-site errors.
Based on the final coordinated 3D substation model, HEEC used Bentley’s digital twin technology to develop a digital twin for visual operational management. “The refined model is imported into the digital twin system, which completes the equipment management, condition evaluation and intelligent warning functions,” said Mr Wang.
Substation digital twin sets benchmarks
Working in an integrated 3D technology environment, HEEC developed a digital, data-driven lifecycle substation solution. Leveraging Bentley’s 3D and reality modelling applications with ProjectWise, the team planned the substation layout, eliminating the demolition of six surrounding houses and reducing the total land area. The ability to perform clash detection avoided over 90% of collisions and 50 reworks, which saved CNY 3 million in costs associated with potential project changes. By establishing collaborative digital design and construction workflows, HEEC reduced the construction period by 30 days.
HEEC has built a full 3D digital twin model of the Xudong 220-kV substation to realise real-time visual monitoring of the substation, enabling full asset lifecycle management, facilitating emergency planning and control, and ensuring safe, reliable operations. The digital twin yields comprehensive, intelligent functions and sets a benchmark for lifecycle 3D digitisation of substation projects for the State Grid Corporation. “The project meets industry needs and serves as a kind of role model for the development of a digital state grid,” said Mr Wang.
All images: Powerchina Hubei Electric Engineering Co Ltd
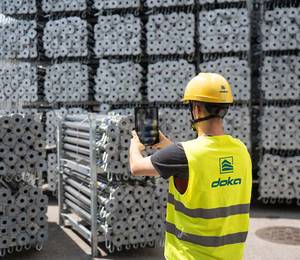
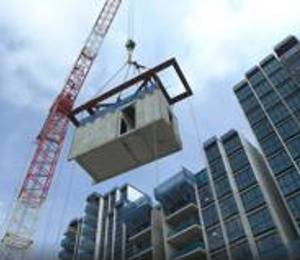
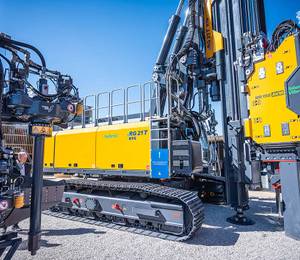
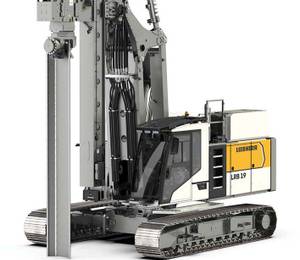
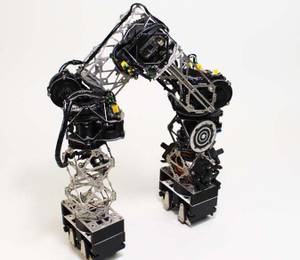
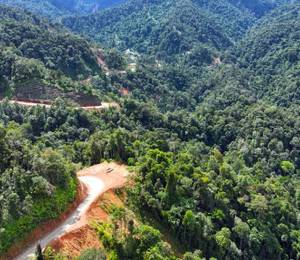
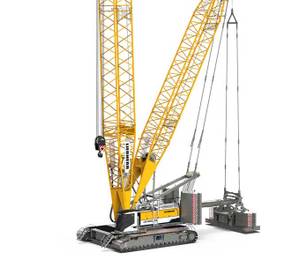