Singapore’s Senior Minister of State for Communications and Information and National Development, Tan Kiat How, has announced that the Built Environment Technology Alliance (BETA) programme will be extended into Phase 2 with an additional S$20 million of BETA Catalyst Funding to support industry-led Research & Innovation (R&I) efforts from progressive and committed BE alliances.
Introduced in 2020, Phase 1 of the BETA programme was led by progressive, needle-moving built environment (BE) sector firms that were ready to commit resources and pursue promising technological advancements in key construction domains.
An example is a project undertaken by the Construction Technology Innovation Laboratory (CTIL) that was launched by Woh Hup (Private Limited) and the Singapore Institute of Technology (SIT) in January 2021. The project ‘Innovative Construction Technologies for Deep Foundation and Excavation’ which comprises three sub-projects, seeks to develop an ensemble of underground construction technologies.
This project is carried out by Woh Hup in collaboration with its three value-chain partners – NatSteel Holdings Pte Ltd, TTJ Design & Engineering Pte Ltd and SEN SG Pte Ltd.
“CTIL addresses a critical, yet relatively under-researched segment of the construction industry. This is a segment that will be increasingly important as Singapore intensifies its land use, and as we try to maximise the potential of underground space, already heavily utilised for underground roads and MRT networks,” said Mr Tan.
“We are constantly exploring innovative solutions that can translate into improvements in the construction process. We have partnered SIT in several research projects prior to setting up CTIL but there are limitations to what we can achieve on our own,” said Woh Hup’s executive director, Yong De-Rhong.
“We believe that the CTIL provides a common platform to better engage industry experts and like-minded partners to work collaboratively to develop capabilities and bring forth positive transformation of the BE sector.”
“This project exemplifies a long-term collaborative model for R&I, that will show the way forward for the rest of the industry,” said BCA CEO, Kelvin Wong.
“Woh Hup recognises that transformation requires the success of all players, as each construction project is dependent on the collective expertise of a long and complex value-chain of partners and today’s research project agreement (RPA) signing ceremony formalises their mutual partnerships on this project.
“The Building & Construction Authority (BCA) hopes to encourage more forward-looking firms to adopt the same mindset and model when embarking on R&I.”
BCA explained that progressive firms that make significant investments in R&I can build long-term capabilities and a competitive advantage. “For example, this project is expected to deliver savings in a critical and relatively under-researched segment of underground civil engineering works as well as improve productivity and on-site safety. The construction cost associated with basement works can range between 4.5% - 20% of a project’s total development cost.”
In public infrastructure projects, the cost of underground works can easily exceed 50% of the total cost, added BCA. “The research being carried out could have a deep impact on the BE sector by transforming the way we build.”
‘Innovative Construction Technologies for Deep Foundation and Excavation’
CTIL focuses on applied research for emerging and innovative technologies for building structure and sub-structures. Woh Hup has committed S$2 million to set up the facility and support its overall operations and projects over five years.
The ‘Innovative Construction Technologies for Deep Foundation and Excavation’ project combines research in inter-related areas to bring about a systems-level productivity improvement across three sub-projects that features one industry collaborator working on each.
One of the sub-projects is ‘Innovative Earth Retaining and Stabilising Structures (ERSS): Post-tensioned Waler System’, with SEN SG Pte Ltd as industry collaborator.
The sub-project’s ERSS makes use of an innovative configuration to reduce the need for intermediate supporting structures, thus increasing working space and resulting in improved site productivity. This initiative is expected to result in 25-30% cost savings in civil and structure works.
Building on proprietary technology developed in South Korea, the project will also customise the ERSS to suit local conditions, with enhanced safety and built-in redundancy.
Another sub-project is ‘High Performance Plunge-in King Post for Top-Down Building Construction’, with TTJ Design & Engineering Pte Ltd as industry collaborator.
This sub-project will develop high performance steel (HPS) king posts that are up to 57% lighter than conventional king posts, and proposes solutions to automate the manufacture of HPS king posts. The reduction in weight and time-savings during the manufacturing process is expected to result in 10-12% cost-savings from fabrication to installation.
A cost-effective and simple to use smart positioning system will also be developed to guide the installation of king posts. This is anticipated to reduce installation time by approximately 20 days and save up to 1,000 man hours for a mid-sized project using 100 king posts.
The third sub-project is ‘Economic Corrosion-Resistant Concrete for Deep Foundation Elements with B600 Rebar’, with NatSteel Holdings Pte Ltd as industry collaborator.
Through investigating various additive proportions, this sub-project aims to develop an optimal and cost-effective novel concrete that is crack and corrosion resistant, enabling the use of Grade 600 reinforced concrete. Such an initiative will also simulate the design performance of the concrete under different underground conditions, for use in deep foundation works.
If Grade 600 reinforced concrete is successful, this could result in up to 20% reduction in steel tonnage, leading to a 15-20% improvement in construction productivity.
All images: BCA
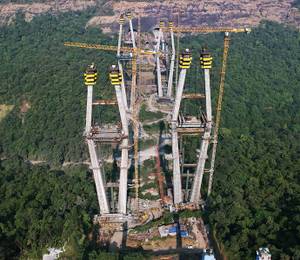
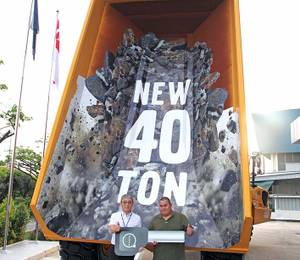
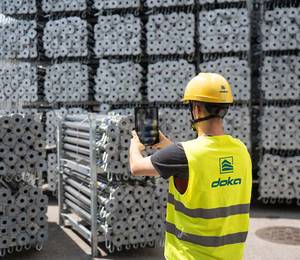
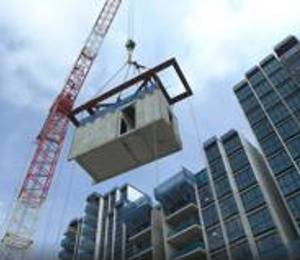
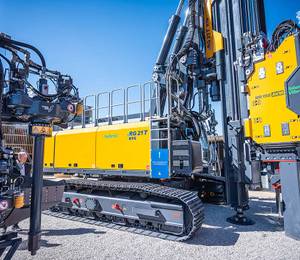
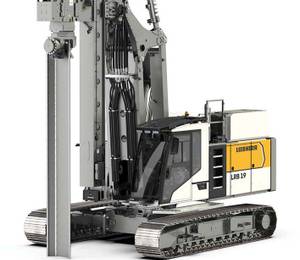
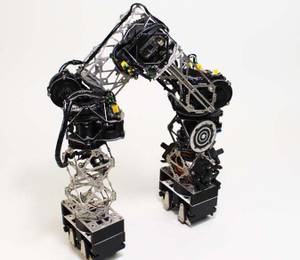