With its heritage founded on one of the most famous hydropower schemes in the world, the Snowy Mountains Scheme, SMEC is widely known as a specialist in hydropower – from design and engineering to construction and project management. The company’s work covers small- and large-capacity power stations, between 5 kW and 8,000 MW.
Karen Atkinson, SMEC’s deputy chief operating officer for Southeast Asia and the Pacific, has been part of the hydropower team delivering various iconic projects, including the Snowy 2.0 in Australia and the Ulu Jelai hydropower plant in Malaysia. She shares with Southeast Asia Construction (SEAC) several new – and upcoming – construction methods and technologies to help the industry achieve safer, more sustainable results.
Improved safety with drones
“Drones have revolutionised certain aspects of developing a hydropower project,” revealed Ms Atkinson, who has been involved in the hydropower industry for more than two decades. She is also a global executive committee member at SMEC.
“Light detection and ranging (LiDAR) as a remote sensing method has become the industry standard during the early development stages of a project. Drones fitted with LiDAR system have made this service affordable for smaller hydropower projects, as fixed and rotary wing planes fitted with LiDAR system have a high initial cost which must be added to the cost of the actual area flown.”
Based in Jakarta, Indonesia, Ms Atkinson is a civil engineer. She was recently appointed to the board of the International Hydropower Association (IHA) for the East Asia and Pacific region.
“SMEC uses drones during the construction of projects for progress photography and to measure excavation and placement of material quantities,” continued Ms Atkinson. “Dam safety inspections require the dam experts to access certain parts of the dam, which are not always accessible, such as spillway chutes, steep dam slopes or vertical structure and intake towers.
“Drone photography is the perfect tool to obtain detailed information about any structural or other defects in these hard-to-reach areas, and in the process reduce the safety risk by not having people accessing these areas.”
She also mentioned that remote operated vehicles (ROVs) for underwater applications are highly specialised equipment, supplied worldwide by only a few companies. “Inspections of water conveyance tunnels of hydropower plants using ROVs is a very cost-effective method to perform a condition assessment with limited downtime of the hydropower plant due to not having to dewater and rewater the tunnels.”
Digital twin to ‘visualise project site’
Speaking about digital twin, Ms Atkinson pointed out that it will become “an integral part of the building information modelling (BIM) process. Throughout the lifecycle of an asset, a digital twin can provide better analysis for informed decisions to help improve energy savings, maintenance and performance.”
The technology can be applied to visualise the project site before construction begins. “It allows for a spatial analysis of the site, to ensure that only the necessary area is used during construction.
“A thorough spatial analysis also helps to predict safety hazards and proactively manage them. Different construction sequences can be trialled to see which one is the most efficient, thus enabling the project to stay on schedule and in turn save time and money. By identifying what equipment is to be used during construction, training can be identified and implemented before construction begins.”
She further emphasised the importance of scan-to-BIM method, a relatively new technology that digitalises the existing hydropower infrastructure. “By scanning structures such as a dam or power station, a digital twin can be created. The digital twin can enable the stakeholder to evaluate when mechanical components need replacing thus avoiding failures.
“By monitoring operations, improvements can be made to performance, resulting in reduced downtimes. By simulating the day-to-day operations of an existing plant, it can be determined where maintenance issues are likely to occur. This helps to predict the operational life of the plant and its components as well as its structural integrity. The improved and targeted maintenance leads to an increase in the lifespan of the asset.”
Digital twin can also be applied in the design of new hydropower plants. “From the outset, the client can communicate to the consultant what the operational outcomes are and the required data to deliver those outcomes. This data can then be built into the digital twin,” explained Ms Atkinson.
“With the use of technologies like artificial intelligence (AI), machine learning (ML) and virtual reality (VR), numerous design options can be simulated to test the generation, transmission and distribution systems. Optimising the design and construction process will help to minimise the projects’ carbon footprint and result in a more sustainable asset for the long term.”
In terms of engineering software, they are also being “improved in leaps and bounds and SMEC is certainly a user of these applications,” added Ms Atkinson. “However, hydropower projects are unique and we found that available project management packages do not allow for and capture the core aspects of our projects. SMEC has therefore developed in-house a project management and information system (PMIS) to cater for the specific needs of hydro projects during the construction phase.”
Autonomous machines ‘can reduce accidents’
Another innovation in engineering and construction is the development of autonomous machines, which can be deployed on hydropower projects, according to Ms Atkinson.
“Large hydropower projects, particularly those with a large dam, require the transportation of huge volumes of construction materials such as soil, blasted rock and concrete. A large percentage of this work is confined to the immediate construction area and is also repetitive, but with some adjustments as the construction progresses.
“For example, SMEC is currently involved in a very large dam project where about 50 mil cu m of material have to be excavated and moved on the site, of which 25 mil cu m have to be placed as rockfill in the dam structure. This process will certainly lend itself to autonomous excavation equipment and transport vehicles, which will reduce the number of vehicle accidents due to human error.”
Ms Atkinson said such technology was used for the transport and placement of concrete from the batch plant to the dam on the recently completed Baihetan hydropower project in China. Featuring an installed capacity of 16 GW, it is dubbed the second largest hydropower plant in the world.
Use of eDNA sampling
From the ecological perspective, SMEC’s environment teams in Southeast Asia and the Pacific have been using eDNA (environmental DNA) sampling for a variety of projects in Vietnam and PNG, explained Ms Atkinson.
“eDNA is a leading academic innovation which has been sufficiently tested in the field and is now becoming a viable alternative to traditional ecology surveys. The advantage of using this technique is its power to consistently pick up more species in one-time sampling event, compared with traditional survey methods that are both costly and time-consuming.”
She highlighted that eDNA is an “efficient, non-invasive and easy-to-standardise sampling approach with great potential as a monitoring tool. It involves using advanced molecular biological equipment to determine the presence of DNA collected in samples from the environment.
“In looking for many species over targeting specific species, it is possible to identify what species are present using DNA Metabarcoding. Other DNA methods can identify if a specific species is present (qPCR, droplet PCR) or identify what a species is from a sample (DNA barcoding).”
What does the future hold?
As onshore hydropower plants continue to be in demand across Asia and worldwide, they will have to be constructed in a more sustainable way, stressed Ms Atkinson. “Hydrogen-powered construction equipment should be one of the first technologies to be used on construction sites to reduce carbon emissions. The development of low-carbon concrete will further reduce the carbon footprint of hydropower projects.
“The design for manufacture and assembly (DfMA) method, 3D printing of smaller components, precast and hybrid construction and digital engineering will also minimise cost and construction time.”
On the future of offshore hydropower, Ms Atkinson said the potential to generate electricity by using tidal currents or the power of waves is “enormous.” Nevertheless, it is technically and economically challenging.
“Tidal power stations normally require substantial civil works to block off a bay or a channel between two landmasses and to house the turbines, so the economic viability of such projects is and will always be a key decider – and maybe is the reason why there are only a limited number of these plants in operation,” she noted.
“Many companies over the years have developed different technologies for harnessing wave power, and pilot plants and small-scale commercial plants have been constructed. However, the ocean is a technically challenging environment to work in, construct, operate and maintain such generation equipment.”
Ms Atkinson believes that developers may still prefer to invest in onshore renewable energy projects with lower risk and cost, “but I foresee that offshore hydropower will have an ongoing role to play in the renewable energy market.”
All images: SMEC
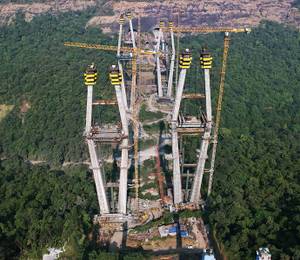
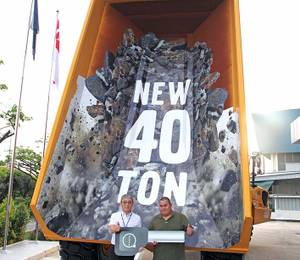
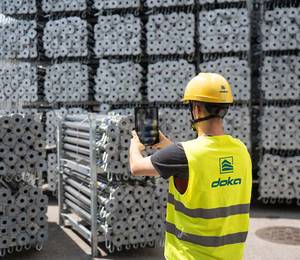
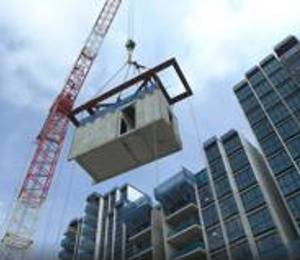
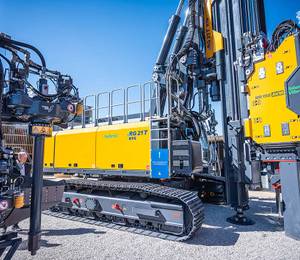
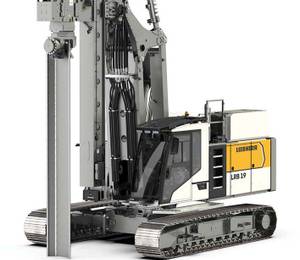
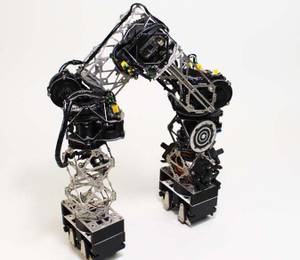