The new Mobiscreen MSS 802(i) Evo from Kleemann is designed for coarse elements. Suitable for natural stone and recycling applications, the screening plant has a feed capacity of up to 500 t/h. It is the successor to the company’s MS 15 Z model.
With its proportionally controlled running gear, the MSS 802(i) Evo can be quickly relocated to the job site (by a low loader) or within the job site. The folding of the side discharge conveyors without the need for disassembly reduces setup times.
Increased application variability is provided by a hopper rear wall that can be folded into three different heights, thus allowing the feeding of crushing plants with a lower discharge height. The large selection of screen surfaces and simple adjustment of the screen parameters, which enable the MSS 802(i) Evo to adapt to a wide range of feed materials, also reduce setup times and in turn save costs.
The plant’s screen casing angle with an adjustment range from 15.4 to 20° optimises screening capacity. The MSS 802(i) Evo is able to perform simple and fast conversion from 3- to 2-way grit, and therefore it can be used to produce and discharge two or three final grain sizes.
An intuitive plant control with automatic start minimises the risk of operating errors and saves learning times. All relevant functions can be operated from a safe distance, improving work safety. Other user-friendly features include easy access options and intelligent cleaning solutions, resulting in less downtime due to maintenance.
In addition, the MSS 802(i) Evo is equipped with a wide crusher discharge conveyor in which the speed can be adjusted, as well as a large material transfer system on the screen deck for optimum utilisation of screening surfaces. Higher discharge heights and stockpiles are also possible, thanks to the optional extended crusher discharge conveyors and telescopic side discharge conveyors.
According to Kleemann, the Mobiscreen MSS 802(i) Evo can be operated through line coupling with all Evo and Pro crushing plants integrated in the process and safety system. Special application flexibility is provided by the stockpile probe required for the process coupling, which can be placed on any discharge conveyor of the plant.
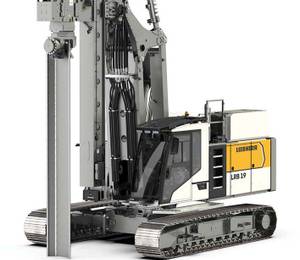
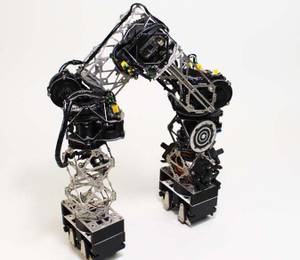
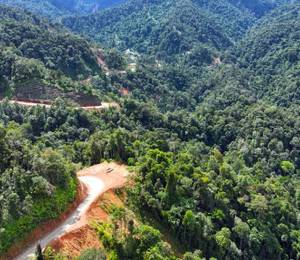
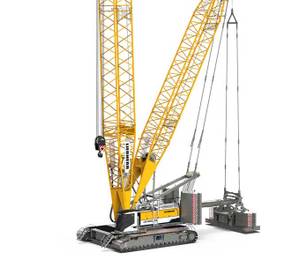
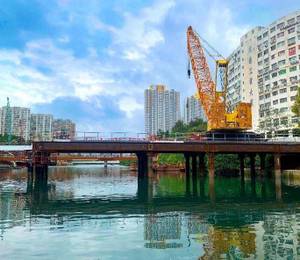
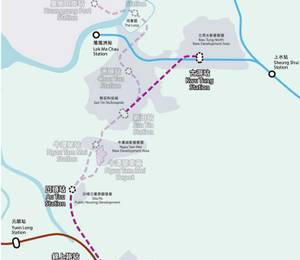
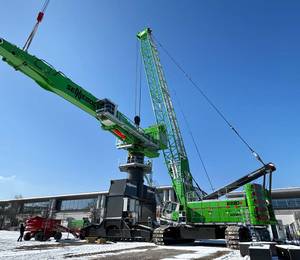