Nestled in the heart of downtown Singapore, the 290-m, 64-storey Tanjong Pagar Centre is currently the tallest building in the country. Developed by GuocoLand Limited, the project is essentially a ‘vertical city’ with a carefully curated mix of office space, retail shops, a luxury hotel, upscale residences and an urban park. Its successful integration of five elements to provide a holistic work-live-play experience won the 2014 World Architecture News Award for Mixed-Use Future Projects.
GuocoLand held the topping out ceremony for Tanjong Pagar Centre in January 2016. In October of that year, the company announced that it has received the temporary occupation permit (TOP) for the office component, Guoco Tower, and the basement retail component of the building. The other components of the project commenced their operations not long after that, in phases.
Skidmore, Owings & Merrill (SOM), a US-based architecture firm, designed the skyscraper, which was built using the top-down construction method - allowing the basement and aboveground levels to be built simultaneously. Contractor on the project was Samsung C&T.
To ensure the 1.7 mil sq ft skyscraper project could meet tight deadlines and stringent material requirements, the project’s developer partnered with concrete experts Pan-United (PanU) and GCP Applied Technologies. “Constructing Singapore’s tallest building was no easy feat,” said Chan Wai Mun, PanU’s director of operations. “The challenge was expediting the construction time and limiting disruption in the congested financial district.”
Top-down construction method
“Given the access constraint of the top-down method, the project required concrete that possessed high flow, long slump retention and good rheology properties, so that kingposts could be inserted later for bore piles before the concrete could set,” explained Shu-Qiang Zhang, GCP’s Asia Pacific technical director.
PanU and GCP assembled a team of scientists, engineers, materials and logistics specialists for the Tanjong Pagar Centre project. The team of product and admixture experts focused on gaining a deep understanding of site conditions, material requirements, delivery timelines, regulatory specifications and safety guidelines, to determine the right concrete product type with the required control flow for the raft foundation.
The interdisciplinary team found the ideal mix using the Concera range of admixtures from GCP along with PanU’s self-compacting concrete and retention concrete. These specialised concrete mixes met the stringent specifications for high flow and extended slump retention.
“Concrete is a complex material and can be very tricky to get right. For the award-winning Tanjong Pagar Centre we had a team working closely to ensure the customised Concera admixture for PanU’s mix had the perfect chemistry,” said Mr Zhang. “Concera admixtures - formulated to deliver consistent, segregation-resistant control flow concrete - did not disappoint.”
The top-down construction method also made the site conditions particularly challenging because it restricted the local concrete discharge point and limited the opening access to the basement mass foundation slab. The six pump trucks housed on-site further exacerbated the space limitation. Plus, the nature of the concrete allowed the team only a workability period of three hours.
“Working closely with GCP, we easily overcame these obstacles,” said Mr Chan. “We also devised a seamless concrete production workstream to ensure that the appropriate quantities of pre-approved materials were on standby throughout the duration of the entire project.”
Concreting gigantic raft foundation
Another project challenge was pouring more than 13,500 cu m of concrete - enough to fill five Olympic-sized swimming pools - to create the building’s gigantic raft foundation. This 3,814-sq-m foundation reportedly required one of the largest concrete foundation pours in Southeast Asia.
For such a massive amount of concrete, it was vital to ensure that the concrete met stringent material and workmanship specifications - from temperature, durability, mix design and performance to pour preparation, delivery timeline, safety and access.
“To ensure quality and consistency throughout the entire casting process, daily plant trial of actual batching were carried out to determine the ease of repeatability,” said Mr Chan. “All concrete batches were closely inspected at the batching plants for flow and temperature before dispatch. Any batch that did not meet the high standards were corrected or rejected.”
On 3 May 2014, the team began concreting the mega raft foundation, which lasted for two days. During the record-breaking 44-hour continuous pour on site, the concrete mix flowed easily in a controlled manner under the force of gravity. The segregation-resistant concrete mix also offered substantial environmental benefits — noise pollution reduction. Since the concrete fills irregular voids quickly, it eliminates the use of loud mechanical compactors, which are typically used to smoothly spread and compact the concrete for a stable foundation.
A large team from PanU and GCP worked seamlessly in 12-hour shifts on site to inspect the concrete for consistent quality and flow. The project required intricate logistics involving 120 mixer trucks, six concrete pumps and one direct discharge chute to deliver 13,500 cu m of concrete from 10 concrete batching plants across the island. The concrete was poured at a steady speed of one concrete truck delivery every 90 seconds and peaked at 531 cu m/hr.
“Customising concrete for the tallest building in Singapore was no small feat,” said Mr Chan. “Thanks to great teamwork between PanU and GCP, we created an accurate mix that not only achieved high flowability but also high quality slump retention.”
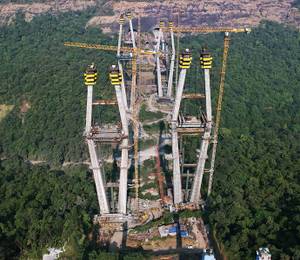
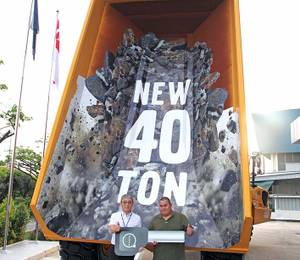
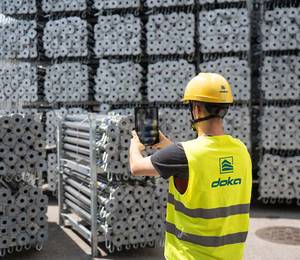
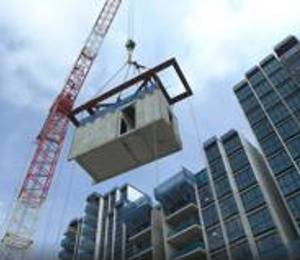
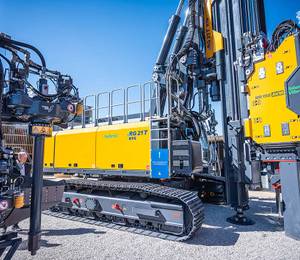
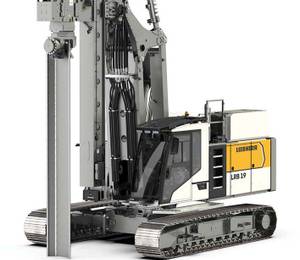
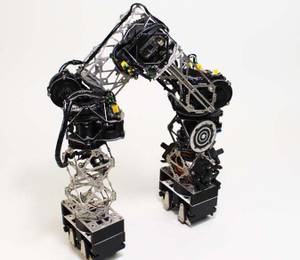