Singapore’s Deep Tunnel Sewerage System Phase 2 (DTSS2) recently marked a new milestone with the completion of its tunnelling works. In this project, Surbana Jurong provided comprehensive engineering services for various aspects of the contract T-11, including deep underground tunnel design, shaft design, ground improvement, hydraulic design, initial and final support, instrumentation and monitoring all the way to aboveground structures. The team was also involved in the operation of a vertical shaft sinking machine (VSM).
The DTSS2 T-11 consisted of 11,500-m-long tunnels with diameters of 3.0 and 3.3 m, as well as 15 shafts and five slurry tunnel boring machines (TBMs). The scope of works for this section included, among others:
1). South Tunnel, its shafts and other features, starting from Shaft Ki located at Keppel Road / Anson Road junction, along Ayer Rajah Expressway (AYE), to Shaft M at Portsdown Avenue / AYE (Shaft Ki to Shaft M). The total length of the South Tunnel is 6 km.
2). Southern Region Link Sewer Tunnel with a total length of 5.5 km, its nine shafts and other features, with the first Shaft L-LS8 located at Sentosa Island to Shaft LW at Warwick Road / Alexandra Road junction (Shaft L-LS8 to Shaft LW).
Shaft excavation with VSM technology
The VSM technology was adopted in the DTSS2 T-11 section, which was the first in Asia for circular shaft construction, revealed Surbana Jurong. It increases the efficiency of excavation in difficult ground conditions.
“It is the inverted form of the conventional, partial face excavation on machines used in horizontal tunnel boring, i.e. from horizontal to vertical,” explained Surbana Jurong. Here, the shaft boring machine operates under water/slurry at a maximum depth of 85 m. All the machine components, such as the hydraulic systems, electrical systems, sealing and lubrication systems, have also been designed to withstand the water pressure at such depth.
According to Surbana Jurong, the VSM technology allows safe and quick shaft construction in difficult ground conditions below groundwater table. This method is suitable for hard rock with an UCS of up to 140 MPa and a hydrostatic pressure of up to 10.2 bar.
Another benefit of the VSM technology is that it enables simultaneous excavation and construction of caisson lining. Plus, the shaft construction can be carried out within a very limited space in densely populated areas, without impacting the existing development or causing severe ground settlements.
Surbana Jurong further highlighted that the DTSS2 tunnels use microbiological- influenced corrosion (MIC) resistant concrete and high density polyethylene (HDPE) lining to protect against corrosion, particularly from bacteria and other microorganisms and also from gaseous fumes in the sewer environment. This sustainability and resilience-driven initiative forms part of the corrosion protection system to ensure the structure is highly durable and will be able to meet the design life of 100 years.
All images: Surbana Jurong
Note: This story has also been published in the Jan/Feb 2024 issue of SEAC (with more images). Click here to read online or here to download the PDF file (pages 38-41).
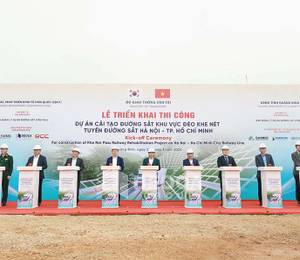
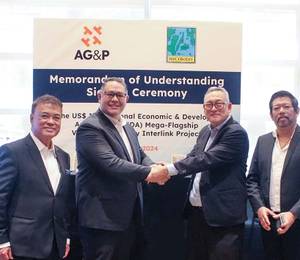
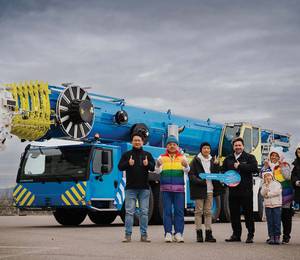

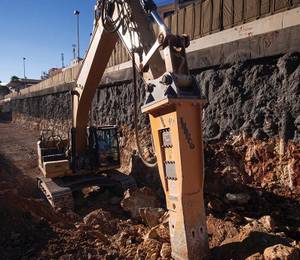
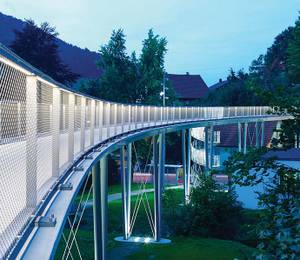
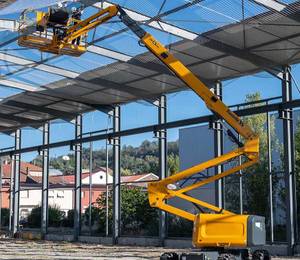
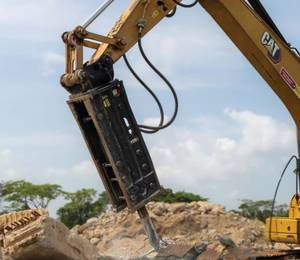
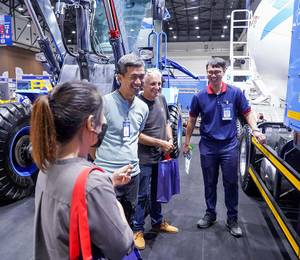
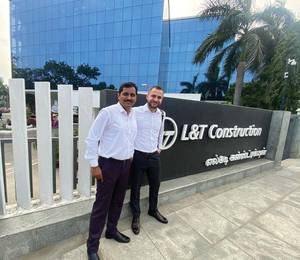