Like many countries around the globe, Indonesia has faced soaring Covid-19 cases that have exceeded hospital bed capacity to treat the affected patients. To address this shortage, the Indonesian government initiated plans to construct 14 new hospitals. PT Wijaya Karya (Persero) Tbk (Wika) was tasked with building one of them on a 22,700-sq-m former football field in South Jakarta.
The US$4 million hospital is a one-storey building with a capacity of 300 beds, 35 intensive care unit rooms, and 10 emergency rooms. It is a modern facility equipped with a negative pressure isolation system to prevent the flow of virus-contaminated air, eliminating the spread of infectious pathogens to the surrounding environment, and includes a robotic nurse and an integrated command centre to connect it to 65 other hospitals.
Given the critical pandemic situation, the government commissioned Wika to complete design and construction works, as well as have the hospital fully operating, in less than a month. Delivery also needed to be cost-effective and environmentally sustainable. To fulfil these requirements on an incredibly tight timeline, compounded by social distancing requirements, Wika needed innovative technology solutions to coordinate and accelerate engineering workflows and fast-track construction without sacrificing quality.
Integrating modular construction with BIM
As a pioneer in modular construction in Indonesia, Wika strived to push the boundaries of design and construction through its innovative approach. This methodology would not only accelerate construction time to within just a few weeks, but also increase quality, safety, and sustainability by using offsite, factory-controlled processes and lightweight, mostly recycled materials. However, such modular system is challenging to execute, requiring streamlined processes and complex decisions that make conventional design strategies insufficient to meet project deliverables.
As a multidiscipline engineering project, Wika needed to coordinate structural, architectural, and mechanical, engineering, and plumbing (MEP) works to facilitate simultaneous design and construction, and meet the tight delivery schedule. To address these planning, collaboration, and management challenges amid a socially distanced team, Wika sought to integrate its modular construction standards with digital BIM application.
The company’s goal was to accelerate the design review process, manage complexity of design changes during construction, and achieve efficiency in time, cost, and quality using BIM technology to digitally collaborate.
“BIM facilitates the creation of designs that are complex to the construction process, starting from initial digital design to manufacturing workflows in all lines of construction disciplines,” explained Romi Ramadhan, BIM manager at Wika. To implement its BIM strategy, Wika needed interoperable modelling applications and a unified digital platform.
Bentley’s applications help speed up project delivery
Wika established a connected data environment using ProjectWise, and adopted Bentley’s reality modelling and BIM methodology to carry out its modular approach. The company used a quadcopter drone and ContextCapture to capture and process images of the 2-ha project site, creating a reality model of the topographic area.
With OpenBuildings Designer, Wika generated a model of the entire hospital building, including structural, architectural, and MEP elements, as well as incorporated landscape and roadway design with OpenRoads. To optimise design of the indoor airflow system to support patient recovery and prevent viral transmission, Wika used Hevacomp to perform airflow analysis and simulation within the building model, designing an HVAC system that complies with proper standards. The company integrated the 3D models with the construction schedule and costs using Synchro 4D while using LumenRT for visual animation, improving construction visualisation for better design verification.
Leveraging Bentley’s interoperable applications, Wika implemented a collaborative BIM methodology, enabling immediate access to real-time data and 3D models without needing to be in the same room. The integrated digital modelling solution facilitated survey, design, simulation, and visualisation, allowing design and construction to occur simultaneously, identifying and resolving design clashes, and making virtual changes to avoid errors and costly rework on site.
ProjectWise and Navigator especially helped coordinate the various, geographically dispersed engineering disciplines resulting in faster decisions throughout the project lifecycle. “The end result is that Bentley Systems can cover the end-to-end processes both in terms of engineering and management,” said Mr Ramadhan.
Working in a connected data environment, 13 multidiscipline BIM engineers collaborated from home, streamlining workflows and increasing productivity to keep the tight project schedule on track - all while following social distancing guidelines.
Establishing industry benchmark
By developing and implementing digital BIM workflows, Wika completed 95 design revisions and resolved 62 clashes in three days to deliver the modular design in only 10 days, saving US$ 400,000. The company used synchro 4D to perform construction simulation and manage the construction process, which reduced construction time by four days to complete construction within 16 days, 20% faster than targeted. This result was extremely important, as it was necessary to have this building completed as soon as possible to provide care to Covid-19 patients.
Working in a unified BIM platform provided complete insight into planning, costs, scheduling, and construction, improving cost efficiency by 18% while optimising quality. Integrating its modular approach with Bentley’s BIM technology, Wika increased its return on investment by 24% and accelerated hospital operations by two months. The ability to extract accurate material quantities from the 3D models - combined with the sustainability of the modular construction process - contributed to saving up to 3,000 cu m of material waste and 10% of project costs.
“Bentley technology has the capabilities and tools to make effective and efficient modular workflows, so we can optimise project costs and improve efficiency of the design process,” said Rizky Yusuf Ramadhan, BIM coordinator at Wika. “We continue to build more and more modular hospitals using Bentley technology as quickly as possible to save more lives.”
The connective data environment also improved visualisation and decision-making without everyone needing to be in the same room, important during the global pandemic. Bentley’s BIM technology played a vital role in modular design and construction, which can slowly shift the world of construction from conventional to digital and industrialise construction project delivery.
Moving forward, Wika plans to expand BIM application and develop a digital twin for lifecycle management of the modular facility, serving as a benchmark for future developments within the industry.
Images: PT Wijaya Karya (Persero) Tbk
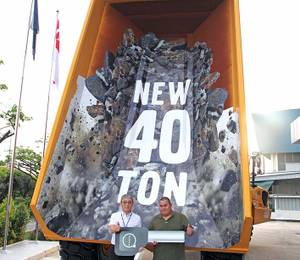
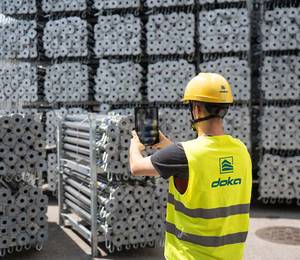
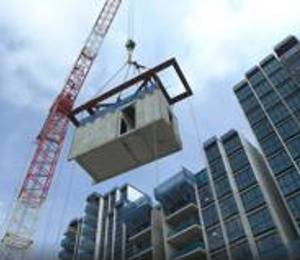
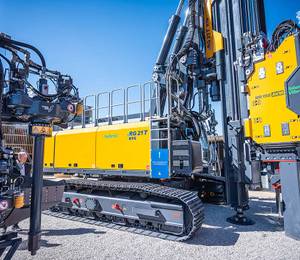
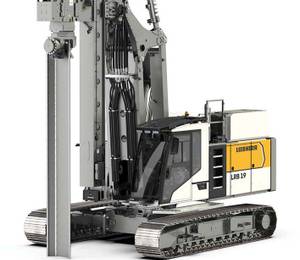
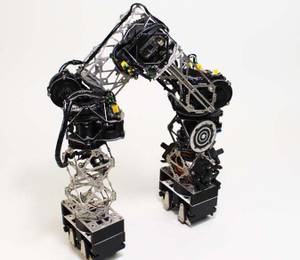
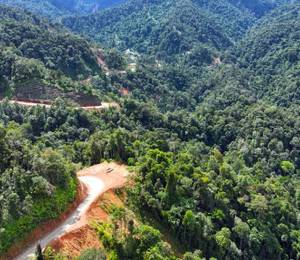