The Excellence Line from Rammer comprises advanced hydraulic hammers that are suitable for all rock breaking requirements. Safety is at the heart of operation across the whole range, whether the hammer is being used in a quarry, on a demolition project, tunnel or any other application.
The upgraded Excellence Line was recently shown at Conexpo 2020. It includes integrated smart technology for easier fleet management and more efficient processes. The latest model in the series is the 9033E, which made its global debut at the show.
Designed for carriers in the 65 t - 120 t range, the 7,400 kg 9033E has all the features found on existing members of the Excellence Line, but in a size and format that delivers the extra punch demanded on major quarrying and demolition projects. Its design allows the hammer to work quietly, with a guaranteed sound level of 131 dB LWA (sound power level of measured 127 dB LWA).
RD3 and MyFleet Telematics service
One of the major developments within the Excellence Line is Rammer’s RD3 remote monitoring device, which is believed to be a first of its kind on hammers. It is now a standard feature on all Rammer Excellence Line hammers, and is also available as an option for Rammer Performance Line hammers and as retrofit-kit for older Rammer hammers.
RD3 is the latest service indicator development from Rammer, using the latest GPS and telematics technology. Additionally, RD3 uses the Rammer MyFleet Telematics service to track and monitor fleet equipment usage without the need to go to site to collect data - ideal for dealers, rental companies, service managers at contractors and operators. This cloud based system enables the hammers to be viewed and monitored via Google maps.
The RD3 remote monitoring device, together with the MyFleet service, is set to become a key component of the equipment rental business. Furthermore, its features improve total utilisation of equipment, of particular benefit in applications where the hammer is part of the process (such as quarrying, mining or tunnelling), and where unscheduled interruption cannot be tolerated.
Hammer lifetime
Operationally, RD3 provides the information that businesses need to get the very best from their hammers. The system enables remote monitoring of total operating hours for new units and comes with a new hammer feature, the ‘hour meter’, linked to the unit’s serial number to measure the exact number of hours it has worked. This enables more accurate invoicing (for example, in the case of hire companies or contractors), proactive or scheduled servicing and enables an accurate value to be set if the unit is sold or traded.
The RD3 system also enables owners and managers of fleets to know exactly where their equipment is and how it is being used. This facilitates better business decision-making, improved security and optimised fleet location, together with enhanced application knowledge and operator support - all accomplished via GPS data, contributing to the overall profitability of the business.
As well as using the MyFleet service, Rammer’s new remote monitoring device also draws heavily on the latest version of its Ramdata system. Rammer has long been considered a pioneer in the field of developing telematic customer-focused solutions, with Ramdata II and now RD3 being the latest in a line of intelligent solutions. According to Rammer, both of the latest introductions have drawn heavily on feedback from customers, dealers and fleet managers, with the system being refined and developed to facilitate a new way of operating.
Apart from RD3, other new features include lower tool bushing rotation and easy replacement in the field, thus increasing lifetime and reducing operating costs. This is further reflected through the use of two tool retaining pins that enhance the lifetime of the tool and retaining pins, also the lifetime of the tool bushings. An IBP on/off selector is fitted to the valve body, resulting in easy field adjustments (available for all medium and large hammers 1655E and upwards) with separate greasing channels from the valve body to the upper and lower tool bushing, further increasing tool/tool bushing lifetime. New, robust plastic wear-resistant plates for optimum hammer protection and noise reduction are also now fitted.
Easy adjustment and replacement
The Rammer Excellence Line has been designed so that it is now even easier to adjust the Idle Blow Protection (IBP) in the field, decreasing both operating and maintenance costs. IBP ensures the hammer cannot be operated until pressure is placed on the tool. It also protects the tool from failure and tie rod stress, reduces oil overheating and protects against premature failures.
In addition, all large Rammer hammers have another ‘easy in the field’ adjustable feature: stroke selector. This allows the operator to optimise hammer operation according to material and application, either to more frequent lower power strokes in softer material or to fewer high power strokes in hard material.
New separate greasing channels from the valve body to the lower and upper tool bushing enable optimum greasing for both bushings, increasing the lifetime of the tool and tool bushings. The latter is achieved due to the upgraded Rammer Ramlube II, an on-hammer automatic greasing device, with separate dozers to adjust optimum grease amounts to tool bushings and an easily changed grease cartridge which provides ease of maintenance in the field. Also, the rotation or replacement of the lower tool bushing in the field is now done by removing the easy-to-use pin. The replaceable lower tool bushing decreases any maintenance costs while also reducing cost of ownership and operating costs.
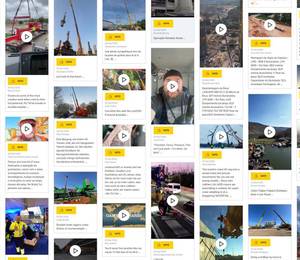
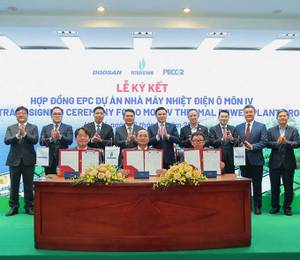
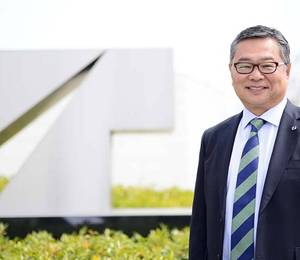
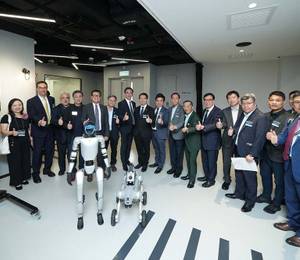
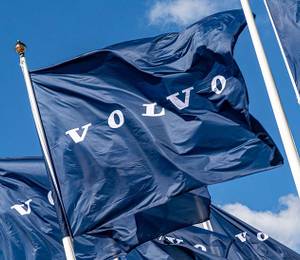
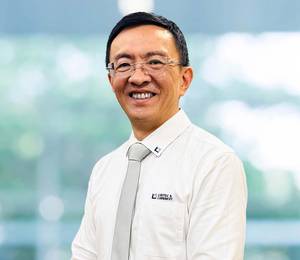


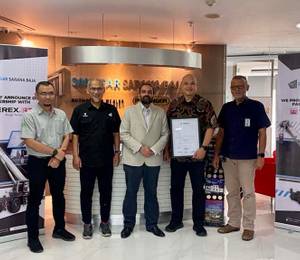
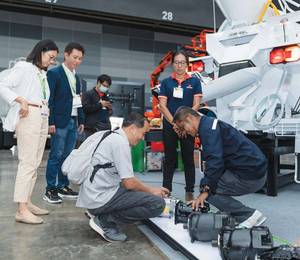